Hydraulic oil is the lifeblood that powers hydraulic machinery and equipment used in a broad range of industry sectors around the world. Hydraulic fluid provides the pressure needed to hydraulic systems through hoses with quick couplings at connection points. There are many reasons why contamination may occur in a hydraulic system, which could create minor disruptions or cause major equipment damage and extended downtime.
Contamination in Hydraulic Systems: The Aftermath
Preventing contamination in hydraulic systems should always be a top priority of equipment operators and maintenance technicians. According to an article in Hydraulics & Pneumatics, 65% to 90% of all hydraulic system failures are caused by contamination as reported by industry experts. With numbers like that, preventing contamination in the first place is critically important to prevent costly consequences.
The aftermath of contamination in a hydraulic system can range in severity from causing intermittent malfunctions to expensive machinery damage with complete equipment downtime. Hydraulic fluid contamination could cause:
- Costly equipment repairs
- Loss of efficiency
- System flushing
- Catastrophic failure
- Equipment downtime
From minor inefficiencies to total equipment downtime, anytime your equipment is out of service, lost productivity negatively affects profitability. Regardless of the severity of equipment damage or failure, extensive troubleshooting is required to determine the cause of the contamination and hydraulic system failure.
What Causes Contamination in Hydraulic Systems?
There are many different possible sources of contamination in hydraulic systems. It is important to know the potential sources to deal with contamination effectively. Some of the most common causes of hydraulic fluid contamination include:
During production of hydraulic fluid – while it is rare due to strict quality controls, contamination during hydraulic fluid production can occur during mixing or processing. It is a good idea to filter all hydraulic fluid entering into a hydraulic system as even fresh hydraulic fluid could be contaminated.
Contamination during hydraulic fluid storage – of course you should always keep hydraulic fluid storage containers tightly sealed at a controlled temperature. Changes in temperature can create thermal expansion or allow moisture to access the interior of storage containers. Moisture contamination is not easy to notice visually but can significantly impact performance.
Contamination during handling and fluid transfer – anytime hydraulic fluids are exposed to the air, it is exposed to moisture, dust and airborne particles. Contamination will most definitely occur if the equipment and the area where fluid transfer is taking place are not clean. Never leave the lid off of fluid any longer than you need to and do not open fluid in an area that is not clean.
Contamination of fluid during maintenance and service – hydraulic fluid naturally degrades over time, requiring regular service intervals. Seals should be checked as leaking seals can be a source of contamination. Maintenance on hydraulic equipment provides an opportunity for many errors to allow contamination to occur. The best thing that maintenance technicians can do to prevent fluid contamination during preventive or repair maintenance procedures is to follow a meticulous checklist and always be aware of the possibility of contamination.
How to Prevent Contamination in Your Hydraulic System
All components should be thoroughly cleaned during each maintenance procedure, all hoses, hydraulic fittings and adapters should be handled carefully with a clean, lint-free cloth. Use dust caps on quick couplers and cap hoses as soon as they are opened. Do not open new filters or seals until they are ready to be used. Remember to always flush the system before adding fresh fluid, and always filter fluid before adding to your hydraulic system.
Flat Face Quick Couplers Limit Contamination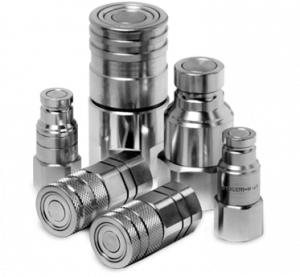
You can additionally reduce your risk of contamination in your hydraulic circuit by using flat-face hydraulic quick couplers, which limit contamination in any hydraulic circuit and are easy to clean. Stucchi offers a wide selection of flat face hydraulic quick couplers with easy connect under pressure, no leak performance and easy cleaning features.
Stucchi’s flat face quick coupler design set the ISO 16028 industry standard. You can find many Stucchi flat face quick couplers to meet your needs or ask a hydraulic specialist.
Our VUZ check valves help prevent backflow and keep fluid moving in the right direction. Stucchi’s hydraulic adapters and check valves are especially helpful in vertically structured circuits, preventing backflow from gravity if or when the pump stops.
Stucchi offers more than 60 years of experience in providing hydraulic solutions to a wide range of demanding industries including construction, demolition, oil and gas, agricultural, mobile, aerospace ground service support and more. If you are experiencing contamination in your hydraulic system, let the hydraulic specialists at Stucchi evaluate your process for a better solution.