Table of Contents
- 1 Hydraulic Quick Couplers: Crucial for Hydraulic System Performance
- 2 The Critical Importance of Hydraulic Pressure Drop
- 3 Understanding Pressure Drop in Hydraulic Systems
- 4 What are the Reasons Causing Pressure Drop in Hydraulic Systems?
- 5 Estimating Pressure Drop in Hydraulic Systems
- 6 Critical Consequences of Pressure Drop in Hydraulic Systems
- 7 Stucchi Solutions and Pressure Drop Analysis
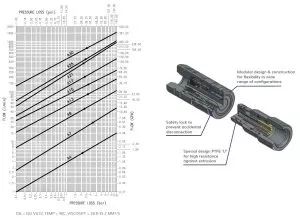
The hydraulic quick couplers on mobile and industrial equipment are just one component of many in a complex hydraulic system, although they are pivotal to system efficiency and reliability.
Understanding how quick couplers contribute to the performance of hydraulic machinery and equipment is critical, and understanding hydraulic pressure drop is vital to prevent system failure and safety issues.
Hydraulic Quick Couplers: Crucial for Hydraulic System Performance
Hydraulic quick couplers are often overlooked, yet they are as crucial to the design of hydraulic systems as pumps, actuators, and valves. These components play a pivotal role in enhancing the overall efficiency and reliability of hydraulic systems across various applications. Their importance in maintaining system integrity and functionality cannot be understated.
The key functions of hydraulic quick couplers are:
- Ensuring a secure connection with the intended component port
- Withstanding system pressure without failing
- Facilitating adequate fluid flow with minimal pressure drop in hydraulic systems
Standard practice dictates ensuring a proper fit and the ability to withstand system pressure. The final point, however, analyzing the hydraulic pressure drop, is often overlooked. Neglecting this can lead to costly consequences in terms of equipment performance and cost.
The Critical Importance of Hydraulic Pressure Drop
At the heart of ensuring optimal performance in such systems lies the concept of hydraulic pressure drop—an often underestimated yet critical factor. Hydraulic hose pressure drop, essentially the difference in fluid pressure between two points within a system, can significantly influence hydraulic system performance.
Stucchi hydraulic specialists can help to demystify pressure drop, from its fundamental principles to practical estimation techniques. It is important to understand the implications of pressure drop in the selection and design of hydraulic quick couplers.
Understanding Pressure Drop in Hydraulic Systems
By understanding and accurately assessing pressure drop in hydraulic systems, designers and operators can enhance equipment functionality, balance cost with performance, and prevent potential system failures, making it an essential topic for anyone involved in hydraulic system design and maintenance.
Pressure drop refers to the reduction in fluid pressure as it moves through different parts of a hydraulic system. This change in pressure is a critical parameter for hydraulic system design and can affect everything from system efficiency to operational costs.
VIDEO – Understanding and Estimating Pressure Drop
What are the Reasons Causing Pressure Drop in Hydraulic Systems?
Equipment operators often want to know what the reasons are for causing pressure drop in hydraulic systems. To fully grasp its impact, it’s essential to understand both the factors and components that contribute to hydraulic system pressure drop. When performing hydraulic pressure drop troubleshooting, consider the following factors:
Factors Affecting Hydraulic Pressure Drop:
- Type of Fluid (Viscosity): Thicker fluids, or those with higher viscosity, resist flow more than less viscous fluids, leading to higher pressure drops.
- Friction and Hose Wall Interaction: As fluid rubs against the internal surfaces of hoses and pipes, it loses energy, resulting in a pressure drop.
- Hose Assembly Length and Diameter: Longer hoses increase the surface area where friction occurs, exacerbating pressure loss. Conversely, a larger internal diameter reduces fluid velocity, thereby decreasing hydraulic hose pressure drop.
- Fluid Temperature: Warmer fluids have lower viscosity and flow more easily, reducing pressure drop. Colder fluids, being more viscous, can significantly increase hydraulic pressure drop.
- Flow Rate: Higher flow rates push fluid through a system more rapidly, which can increase pressure drop in hydraulic systems, particularly if the hoses or components are not adequately sized.
Components Contributing to Pressure Drop
- Hoses, Tubes, and Pipes: The length, diameter, and roughness of these components directly affect the hydraulic hose pressure drop. Smoother internal surfaces and wider diameters can help minimize pressure losses.
- Quick Couplers and Hydraulic Adapters: The design of these components, especially the geometry of fluid passages, can significantly influence pressure drop. Quick disconnects with sharp bends or narrow passages restrict flow and increase hydraulic pressure drop.
- Valves and Other Fittings: Any component that fluid must pass through can contribute to hydraulic system pressure drop, especially valves which regulate flow and can create significant resistance when partially closed or misaligned with the flow direction.
Understanding these factors and how they interact within a hydraulic system is crucial for designing efficient and effective equipment. By carefully selecting and designing each component with pressure drop in mind, engineers can optimize hydraulic systems for both performance and cost efficiency.
Estimating Pressure Drop in Hydraulic Systems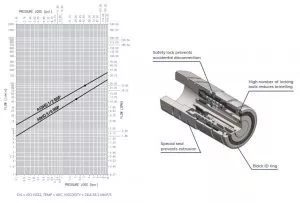
Accurately estimating the pressure drop across hydraulic components is crucial for designing efficient systems and selecting the appropriate hardware. Manufacturers like Stucchi provide hydraulic pressure drop calculator solutions with detailed data and charts that can guide you through this process. Here’s a step-by-step guide on how to calculate pressure drop in hydraulic systems effectively.
Using Manufacturer Data and Hydraulic Pressure Drop Calculators
- Select the Product Series: Begin by identifying the specific product series within Stucchi’s catalog. This is crucial as each series will have different characteristics affecting the pressure drop.
- Estimate the Expected Flow Rate: Determine the flow rate required for your application. This is a critical factor as hydraulic hose pressure drop increases with higher flow rates through the same size component.
- Refer to the Pressure Drop Chart: Locate the flow rate on the vertical (y-axis) of the pressure drop chart provided in Stucchi’s catalog. Draw a horizontal line from this point across the chart to aid in visualization.
- Determine Size Based on Flow Rate and Pressure Drop:
-
- If a specific size has been pre-selected, find where this size intersects with your previously identified flow rate line. From this intersection point, read directly down to the horizontal (x-axis) to find the expected hydraulic pressure drop.
- If the size has not been determined, start from the acceptable pressure drop value on the horizontal axis. Move vertically upwards to meet your flow rate line. The size indicated to the left of this intersection is likely the optimal choice for minimizing pressure drop while meeting flow requirements.
Considerations for Accurate Estimations
- Impact of Viscosity and Temperature: The hydraulic hose pressure drop calculator charts are typically based on tests conducted with a standard fluid (32 cSt oil at 40°C) according to ISO 16028 specifications. If your system uses a fluid with significantly different viscosity or temperature characteristics, these factors could alter the hydraulic pressure drop substantially.
- Consulting with Technical Representatives: For fluids that deviate from the standard testing conditions, or for complex systems where multiple factors influence pressure drop, it is advisable to consult with a technical representative from Stucchi. They can provide insights and data specific to your medium and operating conditions, ensuring that your estimations are as accurate as possible.
By following these steps and considerations, you can effectively estimate the pressure drop across various components in a hydraulic system, allowing for better system design and component selection. This method ensures optimal efficiency and performance, tailored specifically to your hydraulic needs.
Critical Consequences of Pressure Drop in Hydraulic Systems
Ignoring the analysis of pressure drop within hydraulic system design can lead to several detrimental outcomes. Understanding these consequences can emphasize the importance of meticulous planning and assessment in the early stages of system design.
Here are the major impacts of neglecting hydraulic pressure drop considerations:
Reduced System Efficiency and Performance
- Direct Impact on Functionality: When pressure drop in hydraulic hoses is not adequately accounted for, the hydraulic system may not operate at its intended efficiency. Components might not receive the necessary power to perform optimally, leading to sluggish response times and decreased overall system performance.
- Compromised Component Functionality: Excessive pressure drop can lead to a situation where actuators and other hydraulic machinery do not receive enough pressure to function properly. This can severely limit the capability of the entire system to perform its designated tasks.
Increased Energy Consumption and Operational Costs
- Higher Power Requirements: To compensate for high pressure drops, pumps in hydraulic systems often need to work harder, which requires more power. This not only increases energy consumption but also leads to higher operational costs.
- Maintenance and Downtime: Systems that are constantly overworked due to high pressure drops are more prone to wear and tear. This results in increased maintenance costs and potential downtime, which can be costly in terms of both repairs and lost productivity.
Potential Equipment Failures Due to Inadequate Sizing or Excessive Pressure Drop
- Component Stress and Failure: Components that are consistently subjected to pressures beyond their design specifications may fail prematurely. This includes hoses bursting, seals leaking, and fittings breaking, which can lead to catastrophic system failures.
- Safety Hazards: The failure of hydraulic components due to inadequate pressure management can also pose serious safety risks, particularly in industries where hydraulic equipment operates under high loads or in critical applications.
The repercussions of neglecting hydraulic pressure drop analysis are far-reaching, affecting not just the operational efficacy but also the economic and safety aspects of hydraulic systems. Engineers and designers must, therefore, prioritize accurate pressure drop calculations and system testing to ensure that all components are correctly sized and capable of handling the expected pressures. This proactive approach not only safeguards the equipment but also optimizes system performance and longevity.
VIDEO – Understanding and Estimating Pressure Drop
Stucchi Solutions and Pressure Drop Analysis
When hydraulic fittings are undersized, the additional energy required to overcome flow restrictions reduces the energy available for actual work. Pressure drops of hundreds of psi, due to excessive elbows, connections, or undersized fittings, can significantly impair equipment performance. Conversely, using oversized fittings can mitigate flow restrictions but may also increase the size and cost of the system. An increase in coupler size can address these costs by enhancing efficiency.
Contact Stucchi to speak with an experienced hydraulic specialist for professional hydraulic pressure drop troubleshooting.
We can provide the proper planning and diligent pressure drop analysis to ensure that your couplers are appropriately sized, balancing flow rate with cost to meet your design requirements. Hydraulic couplers equipped with soft sealing technologies, such as O-rings, ensure a reliable, leak-free connection, minimizing the potential for leakage. Stucchi provides auxiliary kits and tailored hydraulic solutions that satisfy the specific demands of mobile and industrial equipment, and other hydraulic applications.
Stucchi offers specialized kits and tailored hydraulic solutions that cater to the design needs of your hydraulic system. Our team of hydraulic specialists is ready to assist machinery designers and operators in selecting the optimal quick couplings and adapters to manage pressure drop effectively. Contact us to learn more about enhancing your hydraulic system’s performance and understanding hydraulic pressure drop.